At present, the RTL cage used for raising chickens are mainly welded by cage nets. The cage nets, as the basic material for preparing the RTL cages, have a great influence on the corrosion resistance and service life of the finished chicken cages. At present, the equipment for making cage nets usually adopts welding torch welding, which requires a large number of workers, and the quality of cage nets is different due to the different technical proficiency of workers. Therefore, there are some simple net looms on the market, but the structure is too simple, although the labor of welding workers is saved, but an integrated production line cannot be formed. The current cage net preparation method is: steel wire (cold drawing) – warp and weft weaving net – hot dip galvanizing – preparation of RTL cage – polishing defect. The cage net prepared by this method, after zinc dipping, forms thorn-like lumps after the zinc is cooled, and condenses on all surfaces of the cage net, which not only brings trouble to the subsequent processing, but also easy to assassinate once the treatment is not clean. Personnel or adult chickens may even puncture the eggs, which seriously affects the appearance of the cage net. Moreover, during the grinding process, after the thorn-like bumps are polished off, the corresponding zinc skin is also polished off, resulting in exposed steel wire in the polished part, which makes this part corrode quickly during use and reduces the RTL cage. The service life, so, for the zinc thorn treatment even sometimes involves secondary galvanizing.
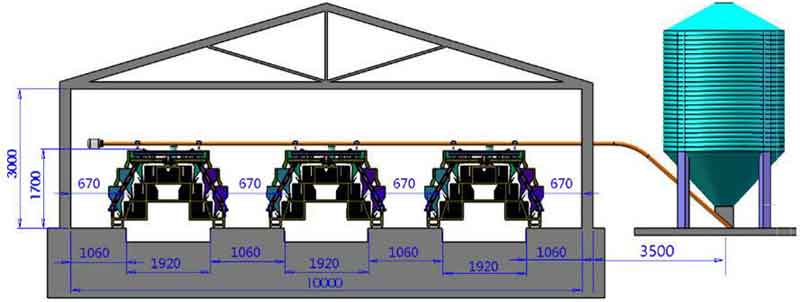
In addition, in the current cage mesh preparation method, a mesh welding machine is used to operate, and the current market welding mesh machine is used in the production of chicken cage meshes, and the degree of automation is not high, and it is difficult to meet the requirements for preparing chicken cage meshes. (For example, the warp is cut according to the size, and it is operated by manpower on the welding table, and then the welding torch is used to weld the weft line one by one, which is labor-intensive and error-prone). In view of this technical problem, there is an urgent need for a simple process, easy to use, one production line from galvanizing to preparing the cage net, high production efficiency and good quality, the surface of the obtained cage net is smooth without zinc thorns, corrosion-resistant , a kind of electro-galvanized cage net production technique with high service life.
Specifications of A type RTL Cage
Cage depth | Cage length | Capacity of one door cage | Capacity of one set of cage | Area per bird | Distance between two frame |
360mm | 390mm | 3 | 90 birds/3 tiers; 120 birds/4 tiers | 468 | 1980mm |
450mm | 390mm | 4 | 120 birds/3 tiers; 160 birds/4 tiers | 438 | 1980mm |
Lifespan | 10-20+ years (cold/hot Galvan) |
Certificates | ISO9001, SGS |
Cage Material | Q235 wire mesh and 275g/㎡cold/hot galvanized wire mesh and sheet |
Poultry House | open house or semi-open house |
Tiers | 3,4 (according to the height of the house and your anticipate farming scale) |
Space for one bird | 430cm² to 470cm² |
Automatic machines | Automatic drinking, automatic feeding, automatic manure removing, automatic egg collecting and automatic climate control |
Age of birds | From 80 days old (0.9kg) to harvest day |